High-Performance Liquid Chromatography (HPLC) is a powerful analytical technique widely used in various fields, including pharmaceuticals, environmental testing, and food safety. However, like any sophisticated technology, HPLC systems can encounter operational issues that can hinder performance. Two common problems are “no pressure” and “high pressure” situations. This article delves into the causes, implications, and troubleshooting strategies for these issues to help HPLC professionals maintain their systems effectively.
Understanding HPLC Pressure Dynamics
Before diving into troubleshooting, it’s essential to understand the normal pressure dynamics in HPLC systems. The pressure in an HPLC system is generated by the pump, which moves the mobile phase through the column packed with stationary phase material. The optimal operating pressure range depends on the specific system and column used but typically falls between 200 to 6000 psi. Monitoring this pressure is crucial for efficient separation and accurate analysis.
Causes of No Pressure in HPLC
Experiencing no pressure in an HPLC system can be frustrating and indicative of various underlying issues. Here are some common causes:
- Pump Malfunction: The pump is the heart of the HPLC system. If the pump fails, there will be no pressure. Common pump issues include:
- Worn Pump Seal: A damaged seal can lead to fluid bypass, preventing pressure build-up.
- Blocked Pump Piston: Debris or wear can obstruct the piston, affecting fluid movement.
- Motor Failure: Electrical issues can result in the pump not operating.
- Clogged Inlet Filter: If the inlet filter is clogged, the flow of the mobile phase can be restricted, resulting in no pressure buildup.
- Empty Solvent Reservoir: An empty solvent reservoir will prevent the pump from drawing in any mobile phase, leading to zero pressure.
- Air in the System: If air bubbles enter the system, it can cause cavitation in the pump, leading to pressure fluctuations or a complete loss of pressure.
- Leak in the System: A significant leak in the system can lead to no pressure being built up. Common leak points include connections, fittings, and the pump head.
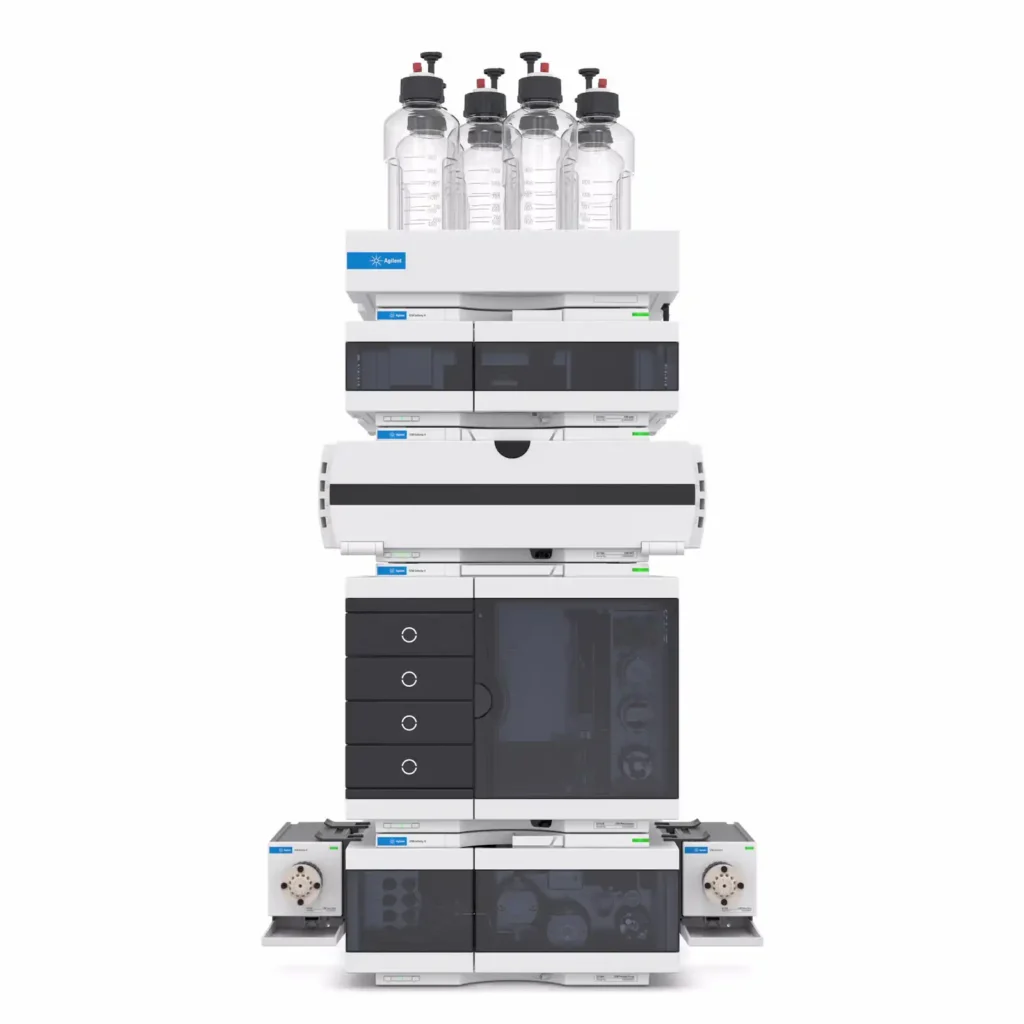
Troubleshooting No Pressure
When encountering a no-pressure situation, follow these steps:
- Check the Solvent Reservoir: Ensure that there is enough solvent in the reservoir and that it is properly connected.
- Inspect the Pump: Look for signs of wear or damage. Test the pump’s operation by running it without the column connected (if possible) to determine if it builds pressure.
- Examine the Inlet Filter: Remove and clean or replace the inlet filter to ensure proper flow.
- Look for Leaks: Inspect all connections and fittings for signs of leaks. Tighten any loose connections.
- Purge the System: Use the purge function (if available) to remove air from the system. Alternatively, manually prime the pump to eliminate air bubbles.
- Consult the Manual: If problems persist, refer to the manufacturer’s troubleshooting guide for specific recommendations.
Causes of High Pressure in HPLC
High pressure in an HPLC system can lead to severe operational issues, including potential damage to the column or the system itself. Understanding the causes of high pressure is crucial for timely interventions:
- Column Blockage: The most common cause of high pressure is blockage in the column. This can occur due to:
- Particulate Matter: Samples containing particulates can clog the column.
- Degraded Stationary Phase: Over time, the stationary phase can break down, leading to an increase in backpressure.
- Incorrect Mobile Phase Viscosity: Using a mobile phase that is too viscous (e.g., high concentrations of buffer or organic solvents) can increase system pressure.
- Pumping Too Fast: Setting the pump flow rate too high can lead to excessive pressure buildup, especially with columns not designed for high flow rates.
- Damaged Column Frit: A damaged frit can restrict flow, leading to increased pressure.
- Temperature Effects: Changes in temperature can affect viscosity and, consequently, pressure. If the system is operated outside its optimal temperature range, it may cause high pressure.
- Fouled or Incorrectly Installed Components: If any components in the flow path, such as filters or fittings, are fouled or installed incorrectly, they can restrict flow and create high pressure.
Troubleshooting High Pressure
If high pressure is detected, take the following steps to diagnose and rectify the issue:
- Monitor Pressure Readings: Regularly monitor the pressure gauge to identify sudden increases that may indicate a problem.
- Check the Column: Remove the column and run the system with a dummy column or a column with known specifications. If the pressure normalizes, the original column may be blocked or damaged.
- Inspect the Mobile Phase: Ensure that the mobile phase composition is appropriate for your column and method. If necessary, dilute the solvent to reduce viscosity.
- Evaluate Flow Rate Settings: Check the pump settings and adjust the flow rate if it exceeds the column’s recommended specifications.
- Examine the Frit and Filter: Inspect and clean or replace the column frit and any filters in the flow path that may be restricting flow.
- Check for Temperature Effects: Ensure that the system operates within the specified temperature range. If temperature fluctuations are detected, consider stabilizing the environment or using a temperature-controlled compartment.
- Regular Maintenance: Establish a routine maintenance schedule for the HPLC system, including regular checks of the pump, columns, and other components. This proactive approach can help identify potential issues before they escalate.
No pressure and high pressure are two common challenges faced by HPLC professionals. Understanding the underlying causes and knowing how to troubleshoot effectively can save time and resources while ensuring optimal performance of the HPLC system. By regularly monitoring the system, performing routine maintenance, and addressing issues promptly, HPLC operators can enhance the reliability of their analyses and contribute to the overall success of their projects.
Maintaining an HPLC system is not just about fixing problems as they arise; it’s about establishing good practices that prevent issues from occurring in the first place. A well-maintained HPLC system leads to consistent results, increased efficiency, and, ultimately, more accurate data. Remember, when in doubt, consult the equipment manual or seek professional assistance to ensure your system runs smoothly.